Carbon Black
Polypedia > ► Materias primas
Negro de humo - Carbon black
¿Que es el carbon black?
Negro de carbono [C.A.S. NO. 1333-86-4] es un carbono elemental virtualmente puro en forma de partículas coloidales que se producen por combustión incompleta o descomposición térmica de hidrocarburos gaseosos o líquidos en condiciones controladas.
El negro de carbono se puede utilizar para hacer un producto opaco, aunque esto solo necesita la mitad del porcentaje de negro de carbono basado en el peso del polímero, comparado con aproximadamente el 3% para la estabilización UV. La función de protección UV del negro de carbón implica proteger la superficie plástica de la radiación, convirtiendo la energía incidente en calor y evitar que los radicales libres produzcan degradación.
Los carbon black se utilizan para ampliar el rango de propiedades físicas para reducir la resistencia química del compuesto. El negro de humo puede definirse en términos generales como agregados de partículas muy finas de carbono, que poseen una estructura molecular amorfa cuasi grafítica Las áreas de distinción más importantes entre negro y negro de horno son el tamaño y la estructura de las partículas. El efecto de un relleno sobre el caucho depende de:
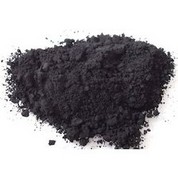
- estructura
- tamaño de partícula
- área de superficie
- características geométricas
Sinónimos
- Acetileno Negro
- Canal Negro
- Horno Negro
- Gas Negro
- Negro de humo
- Negro termal
- Carbon Black
Tipo de negros de humo
El tamaño de partícula promedio de los grados de negro de humo del tipo de caucho disponible comercialmente varía de aproximadamente 10 a 500 nanómetros. Dentro de esta extensión de cincuenta a uno, existe la posibilidad de un gran número de calidades, cada una de las cuales proporciona a la formulación de caucho un conjunto único de propiedades. En general, cuanto mayor sea el tamaño de partícula, menor será el costo y menor será el potencial de refuerzo del material.
- SAF - Horno de Super Abrasión
- ISAF - Horno de Super Abrasión Intermedio
- CF - Horno Conductor
- SCF - Horno Super Conductor
- HAF - Horno de alta abrasión (bajo estructura y alta estructura)
- FF - Horno fino
- FEF - Horno de extrusión fina
- GPF - Horno de uso general
- SRF - Horno semi reforzado
- MT - Medio Térmico
- EPC Easy Processing Channel
Así como el tamaño de partícula promedio es importante, también lo es la distribución de los tamaños de partícula. Las distribuciones del tamaño de partícula pueden ser estrechas o amplias o incluso bimodales, y cada tipo influye en las propiedades del caucho de una manera sutil. Los negros de humo que proporcionan la mayor relación de refuerzo a área de superficie son aquellos que se han producido utilizando el tiempo de reacción más corto
Produccion
Dos procesos de fabricación de negro de carbón (horno negro y negro termal) producen casi todos los negros de humo del mundo, con el proceso de horno negro siendo los más comunes. El proceso de horno negro utiliza principalmente de metano o aceites aromáticos pesados,como materia prima. El horno de producción utiliza un reactor cerrado para atomizar el aceite de alimentación en condiciones cuidadosamente controladas (principalmente temperatura y presión).
El material de alimentación primario se introduce en una corriente de gas caliente (que se logra al quemar un material de alimentación secundario, por ejemplo, gas natural o aceite) donde se vaporiza y luego se piroliza en la fase de vapor. Para formar partículas microscópicas de carbono, en la mayoría de los reactores de horno, la velocidad de reacción es controlada por vapor o agua pu lverizada.
El negro de humo producido se transporta a través del reactor, se enfría y se recoge en filtros de bolsa en un proceso continuo. El gas residual, o gas de cola, de un reactor de horno incluye una variedad de gases tales como monóxido de carbono e hidrógeno.
La mayoría de las plantas de horno negro usan una porción de este gas residual para producir calor, vapor o energía eléctrica. Todos los grados de horno se realizan en un proceso continuo, mientras que los grados térmicos se realizan en un proceso continuo.
Nomenclatura
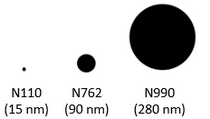
La nomenclatura utilizada actualmente para los negros de humo de grado de goma fue instituida por el Comité D 24ASTM sobre Negro de Carbón en 1968. Se compone de una letra de prefijo seguida de un número de tres dígitos. El prefijo, ya sea N o S, indica si la calidad es un material (N) o un material de curado bajo (S). Cuando se desarrolló el sistema, los canales negros aún se usaban comúnmente y se curaban lentamente. La mayoría (si no todas) de las calidades de caucho actualmente activas llevan el prefijo "N". El primero de los tres dígitos se usa para proporcionar una medida aproximada del diámetro medio de partícula del grado determinado por microscopio electrónico y expresado en nanómetros. ASTM D 24 asigna el segundo y tercer dígito a nuevos productos a medida que los distintos fabricantes los desarrollan.
Efecto reforzador de negro de carbón
El refuerzo de elastómeros por el negro de humo se rige por la morfología del negro y sus interacciones físicas y químicas con el polímero. Estos últimos están fuertemente afectados por la grafitización y la oxidación de la superficie. En los negros de humo modernos con grado de goma, la unión fuerte del polímero a la superficie del negro de humo se ve afectada por varios mecanismos, pero las diferencias químicas en la superficie entre los negros son relativamente pequeñas, de modo que la característica dominante se convierte en la morfología. Esto está determinado por el tamaño promedio y la distribución del tamaño de las partículas que se fusionan para formar agregados primarios que se asemejan a bobinas aleatorias ramificadas, la disposición espacial de las partículas en estos agregados y el número de partículas por agregado y su distribución. Esta morfología altamente compleja puede, en una primera aproximación, estar representado por el área de superficie específica accesible al caucho y alguna medida, generalmente indirecta, del volumen impregnado por los agregados primarios ("estructura"). Las propiedades mecánicas importantes de los cauchos reforzados dependen en diferentes grados de estas dos características, a menudo de manera bastante compleja. La adición de negro de carbón aumenta en gran medida el módulo, la resistencia a la tracción, la resistencia al desgarro, la resistencia a la fatiga, la resistencia al desgaste de los cauchos sin relleno y sobre las propiedades viscoelásticas. Todos los fenómenos mencionados anteriormente, por supuesto, fueron el resultado de llenar el negro de carbón en los cauchos, por lo que estos fenómenos están básicamente conectados entre sí y no se generan de forma independiente. La resistencia a la abrasión aumenta considerablemente cuando se agregan cargas de refuerzo al polímero. Este es, en particular, el caso de las gomas: la incorporación de negro de humo (por ejemplo, 40 partes en peso por 100 partes de goma) aumenta la vida útil de la banda de rodadura de un neumático de 5,000 a 50,000 o incluso 100,000 km. El negro de carbón también se demuestra por su efecto sobre la resistencia a la tracción de los vulcanizados de caucho. Un SBR vulcanizado sin relleno se rompe a una carga de 2 a 3 MPa; con negro de humo la resistencia a la tracción supera los 30 MPa.